Beyond Routine Testing to Support Long-Term Lubricant Life
Advanced Testing of Lubricants Supports Longer Life
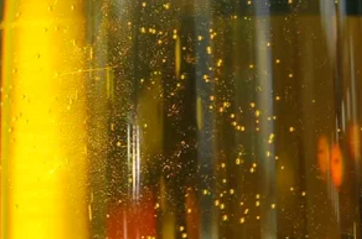
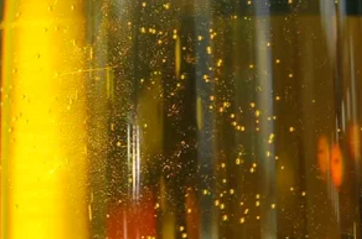
Performing regularly scheduled oil analysis is the best methodology to monitor wear and oil condition. Even under normal operating conditions, wear particles and oil degradation by-products are generated. If abnormal lubricating conditions exist, wear and degradation can occur at an accelerated rate. This makes regularly scheduled oil analysis even more important.
Routine analysis can detect problems such as wear, oxidation, and acidity. However, more advanced testing is needed to detect deterioration in a lubricant’s performance properties such as water separability, foaming management, and varnish prevention.
Wear particles circulating through a lubricant system can be abrasive, generating more wear particles as they rip through a lubrication regime. Left unchecked, elevated concentrations of abrasive debris this will lead to accelerated wear, reduced component life, and increased maintenance. Wounded lubricant properties can adversely affect lubricant performance and, ultimately, your equipment’s performance.
Excessive entrained air causes extreme heat on metal surfaces and will reduce hydraulic performance, cause micro-dieseling, pump cavitation, and other problems. A lubricant’s ability to release entrained air has become increasingly important as newer machines' oil capacity has become smaller, resulting in decreased reservoir dwell time in a circulating lube system.
Water separability is critically important, especially for applications prone to water ingression, such as steam turbines. Prolonged periods of water saturation lead to corrosion and accelerated lubricant degradation. A typical lubricant’s water separability declines as oil degradation occurs. Stand-alone routine oil analysis will not measure whether a fluid’s water separability remains adequate for the application.
Varnish accumulation in a lubricating system has received much attention in recent years due to problems such as filter plugging, increased bearing temperature, valve stiction, and increased scrap rates in plastic injection molding machines. Often a vanishing issue originates from an accumulation of spent oil additives that attract to lubricated metal surfaces once an in-service fluid is no longer able to dissolve an their concentration. Here are some actions you can take to mitigate varnish:
· Targeted Filtration Technology: Use special filters to remove varnish. Electrostatic, resin, and cellulose depth filters (CDF) are the main filters used, and they should be put in place using the correct technology to combat the specific issue in a system. Resin filters work well on R&O oils but are not typically used with AW hydraulic oil due to the potential of removing the ZDDP additive. Electrostatic filters don’t work well with R&O oils but are a viable choice for hydraulic oils. Electrostatic filters were first developed for AW hydraulic oils in plastic injection machines.
· Solubilizers and Re-additization: These may be viable, chemical enhancement alternatives to re-charging the solubility of a used fluid so it can re-dissolve an accumulation of spent additives. Several companies offer these products and provide support regarding which option best fits your requirements.
· Prevention: Consider using varnish-resistant lubricants. If you prefer to change the fluid rather than employ varnish mitigation technology, several lubricant manufacturers provide varnish-resistant fluids.
As the service life of the fluid increases, the antioxidants, which are sacrificial, are gradually depleted. Low levels of antioxidants leave the fluid susceptible to degradation. Monitoring the active antioxidant protection remaining in a used fluid can be performed with the RULER™ test, which uses the linear sweep voltammetry technology to assess remaining active protection of the antioxidant package of a certain lubricant. Changing or partially replenishing the oil can improve the additive level. Re-additization can be an option to changing the oil under the right circumstances.
Increased acidity can lead to corrosion and deposits forming in the system. Phosphate esters are prone to hydrolysis (cleavage by water), producing degradation by-products that are very acidic. Phosphate esters are more expensive than typical hydrocarbon lubricants. Resin filters are utilized to reduce acidity. It's very important to measure for a reduction in a phosphate ester’s resistivity over time, and to understand the condemning limit for call to action. Reduced resistivity (increased conductivity) may lead to electro-corrosion of servo valves.
These are some of the advanced tests commonly performed on industrial oils to monitor internal contamination and fluid condition. Proper implementation promotes much longer fluid life to minimize equipment downtime.